Hace algun tiempo, una columna de Vittorio Corbo comentaba que el crecimiento de nuestro país había sido el fruto de mucha transpiración, pero ante el nuevo escenario que se comenzaba a vivir en nuestro país, ya no teníamos espacio para seguir creciendo a costa de la “transpiración” y para seguir creciendo, lo que se requería era resolver los problemas que limitan los aumentos de productividad usando más la “inspiración”.
Ese ingenioso contrapunto nos motivó a usarlo en este artículo, pero aplicado al ámbito minero, donde claramente muchos de los personajes claves del entorno minero nacional claman por un mejoramiento de la productividad.
De hecho, recientemente en una entrevista de El Mercurio, el máximo ejecutivo de BHP Billiton en Chile, Peter Beaven, comentaba respecto de la necesidad de mejorar la productividad en Chile, dado que en comparación con minas muy similares de Canadá o Estados Unidos, la productividad de la minería chilena era la mitad “Aquí se mueven 40 mil toneladas por persona al año; en Canadá o Arizona, 80 mil a 90 mil toneladas al año. Esa es una tremenda oportunidad, es nuestra obligación cerrar esa brecha de productividad”.
“Aquí se mueven 40 mil toneladas por persona al año; en Canadá o Arizona, 80 mil a 90 mil toneladas al año.”
Peter Beaven, BHP Billiton
Sin duda, estamos de acuerdo con estas visiones convergentes de un connotado economista, académico, investigador, consultor y ex presidente del Banco Central de Chile y de un alto ejecutivo de una de las empresas mineras más importantes de nuestrob país, respecto de la urgencia de abordar -en nuestra minería- la mejora de esa esquiva productividad.
Ante este desafío, y tal como lo confirman las versiones de prensa, respecto de las inversiones cuantiosas que hay que realizar en Codelco los próximos años, existe la mirada de aquellos que ven en los aumentos de inversión, la salida para mejorar la situación de la empresa, pero felizmente no es la única y dada nuestra experiencia, queremos darle a conocer a nuestros lectores otra visión del ámbito del mejoramiento de los procesos productivos y transaccionales y que por concepto no demandan inversión y si lo hacen, son de tipo marginal.
Por esa razón, queremos compartir algunos de los beneficios financieros que se han obtenido -utilizando herramientas de mejoramiento de procesos- en empresas mineras, no sólo de Chile, sino también de Bolivia y en la que debemos ser generales, ya que no podemos dar demasiados detalles que pudieran vulnerar nuestro compromiso de protección de la confidencialidad de los resultados de nuestros clientes.
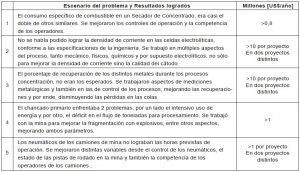
La Metodología DMAIC y el Mejoramiento de Procesos
Desde hace bastante tiempo, algunas empresas mineras como Noranda y BHP Billiton, están abordando los temas de mejoramiento de sus procesos, utilizando en todas sus instalaciones a nivel mundial, la metodología Lean Six Sigma, que en realidad puede utilizarse con distintos focos y profundidad, para privilegiar LEAN (o el Toyota Production System o Just In Time), la TOC (Theory of Constraint), o TPM (Total Productive Maintenance) o todas las anteriores; sin embargo, mantienen la base de lo que inició Motorola por los 90 y que es lo que se denomina Process-DMAIC. Ver gráfico adjunto.
El uso de la aún poco entendida Metodología Lean Six Sigma que usa el macro Mapa de Ruta del P-DMAIC, permite abordar Paso a Paso, los problemas que se presentan en uno o en un conjunto de procesos de una organización. Esta metodología, ha sido la clave para lograr los beneficios ya mostrados en esos y en otros proyectos exitosos del ámbito minero, en los que nos ha tocado participar.
El foco de un DMAIC, es la realización de un proyecto de mejoramiento sobre un proceso que tenga una variable crítica de salida -deficitaria- y que impacte la cadena de valor del negocio minero. La idea es que cada Fase del DMAIC no se cierre hasta que el Gerente Champion, que está direccionando su desarrollo, apruebe el Toll Gate de cada Fase y así sucesivamente.
Lo anterior permite, por ejemplo, que mientras no esté claramente definido el problema a abordar y todos los entregables previstos para esa fase DEFINIR, no se apruebe el paso a la fase MEDIR, que es la más extensa de todas las fases ya que tiene 5 sub-fases por resolver, según se muestra en el DMAIC.
El foco de un DMAIC, es la realización de un proyecto de mejoramiento sobre un proceso que tenga una variable crítica de salida -deficitaria- y que impacte la cadena de valor del negocio minero.
Importancia de la Sub Fase “Análisis de los Sistemas de Medición”
En los más de 14 años de experiencia mejorando procesos mineros, nos ha llamado la atención el débil cuestionamiento que se hace de las mediciones, por ejemplo, se trabaja con métricas del tipo [tons/hora] en el transporte de mineral, entre una sección de la mina y el chancador, pero nos preguntamos ¿Qué tan confiable es esa medición de peso?
La respuesta en este caso puede ser simple, en la medida que las celdas de carga de las palas y de las tolvas de los camiones, estén calibradas, las mediciones van a ser confiables y en eso hay acuerdo.
Pero ¿qué pasa con la Ley del Mineral que va en ese camión? ya que, sin duda, es clave para determinar las eficiencias en la cadena de procesos y que, en su momento, van a impactar los resultados del Balance Metalúrgico del Negocio Minero.
La respuesta en este caso, ya no es tan simple, ya que hay muchos sub-procesos involucrados en esa determinación y cada uno de ellos, aporta variabilidad para el cálculo final de esa Ley y si eso no logra conocerse a cabalidad, los errores pueden ser gravitantes.
Una de las herramientas que se utiliza es el análisis estadístico, que se conoce como Gage R&R y que persigue determinar entre otros, la variabilidad total del Sistema de Medición, que incluye los equipos de medición, que normalmente si están calibrados y son de buena calidad, aportan poco a la variabilidad total.
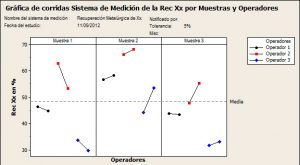
“En los más de 14 años de experiencia mejorando procesos mineros, nos ha llamado la atención el débil cuestionamiento que se hace de algunas mediciones”
Otro aspecto a considerar, es la determinación de la variabilidad que aportan los operadores y sus interacciones, tanto con los equipos como con los métodos que se utilizan para realizar los diferentes pasos que están involucrados en ese tipo de mediciones.
Sólo para citar algunos, el muestreo en la mina, la preparación de la muestra de laboratorio, la secuencia de procesos propios de un laboratorio metalúrgico y finalmente, la determinación en un Laboratorio Químico, según sea el caso.
Se muestra la Gráfica de corridas del Sistema de Medición de una Recuperación, que es parte del Gage R&R. Se prepararon 3 muestras de mineral de distintas secciones de la mina que se entregaron en “forma ciega”, con 2 repeticiones, para que fueran analizadas por distintos operadores de un laboratorio metalúrgico (en este caso sólo se presentan el resultado de 3 de ellos) para determinar la recuperación metalúrgica de interés.
Se puede visualizar que para la muestra 1, mientras el operador 2 (en rojo) determinó, en promedio un 58% de recuperación; el operador 3 (en azul), sólo reportó un promedio de las 2 muestras de 31,5%. Diferencias bastante preocupantes y que, sin duda, no permiten tener claridad respecto de cuál es el operador que está midiendo bien, lo único que se puede concluir con esta gráfica, es que al menos el Operador 1 es más consistente en sus repeticiones.
Este es uno de los temas que se pretende resolver al abordar metodológicamente el mejoramiento de procesos, con las herramientas apropiadas y cubriendo todas las aristas que nos ayuden a tomar la mejor decisión.
Le sugerimos cambiar el énfasis desde la “transpiración” hacia un escenario que sea mucho más proclive a la “inspiración”, con el propósito de ir logrando -paulatinamente- las mejoras de productividad que necesitan nuestras empresas mineras.
Leave A Comment